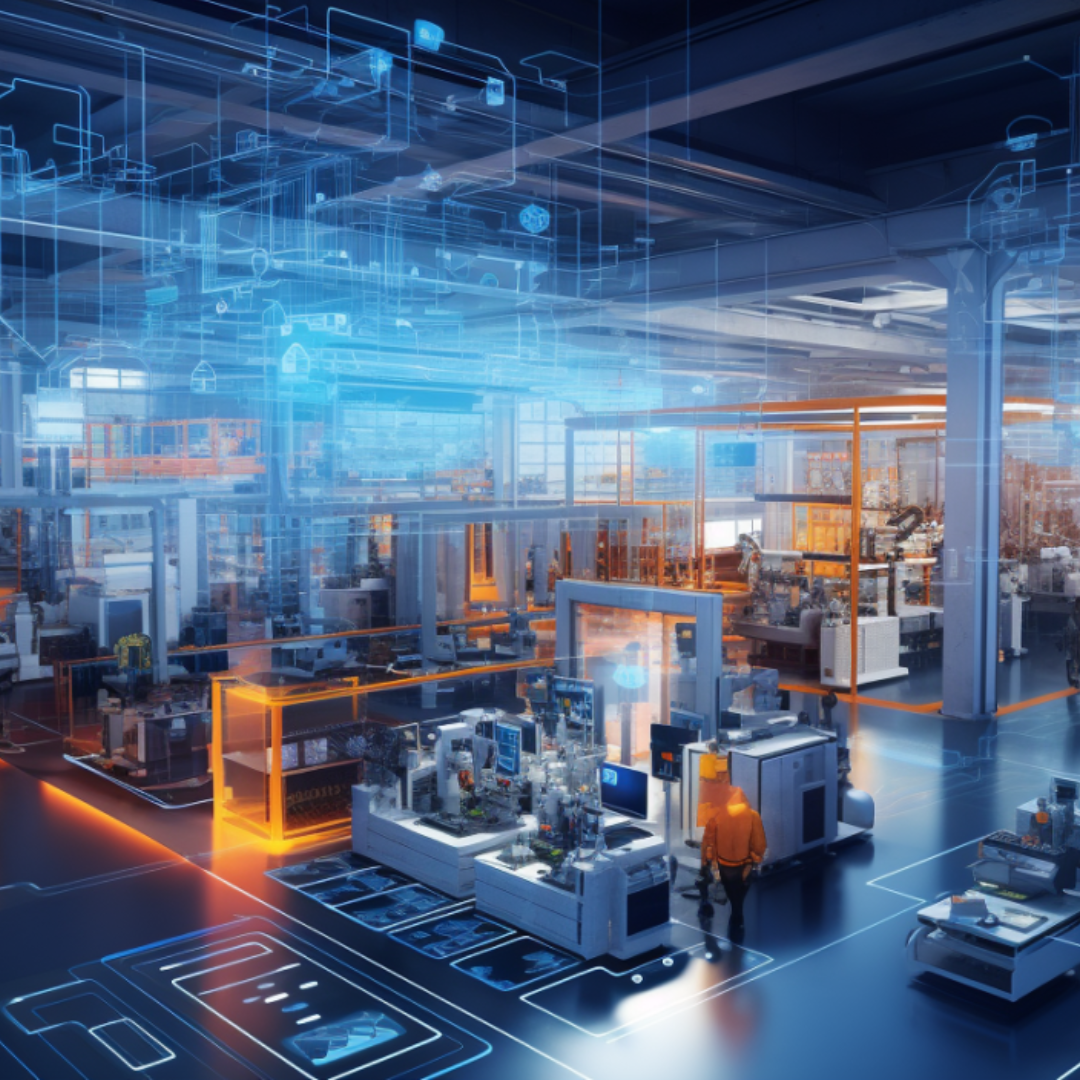
8 Trends Set to Revolutionize the Manufacturing Industry
Introduction
Imagine a shoe company where customers design sneakers from scratch—choosing everything from material to laces—and have them printed and delivered within 24 hours.
What was once a futuristic dream, thanks to 3D printing technology, is now a reality. 3D printing is just one of many innovations reshaping industries, illustrating the rapid evolution of the manufacturing sector.
To put this transformation into perspective, the global market for smart manufacturing technologies is projected to grow from $181 billion in 2021 to over $543 billion by 2030. This growth highlights a massive shift in how manufacturers embrace new tools to enhance productivity, streamline operations, and reduce environmental impact.
From advanced robotics and AI-driven processes to sustainable practices and digital twins, the manufacturing industry is leveraging cutting-edge technology to meet the demands of a fast-evolving global economy. These new approaches not only improve efficiency and reduce costs but also drive sustainability initiatives that are essential for long-term success. For companies operating in diverse global markets, staying ahead of these trends is critical to maintaining competitiveness and innovation.
Here are 8 rising trends reshaping the manufacturing industry.
They provide a global perspective and actionable insights for brands. These insights will help decision-makers navigate the shifting landscape, capitalize on emerging opportunities, and future-proof strategies in a rapidly evolving world.
1. Smart Manufacturing (Industry 4.0)
What is it?
Smart manufacturing, also known as Industry 4.0, integrates IoT, AI, and advanced analytics to create fully connected environments where machines communicate in real-time, optimizing production and efficiency.
Impact of Smart Manufacturing on Modernization
These technologies allow manufacturers to monitor equipment performance, detect issues preemptively, and adjust production in real-time. AI-powered analytics identify patterns that reduce waste, improve product quality, and streamline supply chains. This automation offers the flexibility to adjust production quickly, customize products on demand, and lower operational costs.
Strategic Recommendation for Brands:
Invest in IoT systems and AI-driven analytics to optimize production processes. Implement predictive maintenance to minimize downtime and ensure consistent quality, positioning your brand for growth in a tech-driven future.
2. Additive Manufacturing (3D Printing)
What is it?
3D printing allows manufacturers to produce complex, customized products layer by layer from digital designs, enabling mass customization while reducing material waste.
Impact of 3D Printing on Modernization
Additive manufacturing reduces waste by applying material precisely where needed and accelerates prototyping. It allows rapid, cost-effective customization, enabling manufacturers to meet personalized demands without sacrificing efficiency.
In sectors like aerospace, 3D printing has been instrumental in reducing the weight of components, leading to more fuel-efficient designs. For healthcare companies, 3D printing offers the ability to create customized medical implants and devices that fit the unique anatomy of individual patients, enhancing patient outcomes and reducing costs.
Strategic Recommendation for Brands:
Leverage 3D printing for prototyping and mass customization to differentiate your brand with personalized products while maintaining efficiency and reducing waste.
3. Sustainable Manufacturing
What is it?
Sustainable manufacturing focuses on reducing production’s environmental impact through using renewable energy, eco-friendly materials, and circular economy models that promote reuse and recycling.
Impact on Modernization
Sustainable practices help manufacturers reduce energy consumption, cut emissions, and lower resource usage. Adopting renewable energy sources like solar and wind, alongside waste-reducing initiatives, ensures manufacturers can operate efficiently while meeting consumer expectations for environmentally responsible products.
For companies aiming to future-proof operations, sustainability now drives product design, material sourcing, and overall supply chain strategy.
Strategic Recommendation for Brands:
Adopt renewable energy and circular economy principles to lower carbon footprint and align with consumer demand for sustainable, eco-friendly products. This will enhance your brand’s market position while ensuring long-term operational efficiency.
Japan’s Automotive Industry
Japan has been at the forefront of sustainable manufacturing practices, particularly in the automotive industry, where companies like Toyota and Nissan lead the charge. Toyota, known for its hybrid vehicle innovations, has been working toward achieving zero emissions across its entire vehicle production line by embracing hydrogen fuel cells and expanding its use of solar energy in its manufacturing plants. Toyota’s Motomachi plant is a prime example, where the company has integrated solar panels to power parts of its operations and has committed to water recycling practices to reduce environmental strain.
Similarly, Nissan has implemented its Nissan Green Program, which focuses on reducing CO2 emissions, increasing the use of renewable materials, and minimizing waste during the production process. Using lean manufacturing and energy efficiency programs, Nissan has made significant strides in cutting its environmental footprint. These efforts reflect Japan’s broader commitment to sustainability and showcase how manufacturers can balance innovation with eco-friendly practices.
4. AI and Machine Learning Integration
What is it?
AI and machine learning enable manufacturers to make data-driven decisions, from optimizing production schedules to predicting equipment failures and improving quality control.
Impact of AI and ML on Modernization
AI boosts production efficiency by predicting maintenance needs, minimizing downtime, and enhancing product quality through automated inspections. Machine learning analyzes large data sets to identify inefficiencies and streamline processes.
Strategic Recommendation for Brands
Incorporate AI-powered systems to predict equipment failures, optimize scheduling, and improve quality control, ensuring your brand remains competitive in a data-driven manufacturing landscape.
India’s Predictive Maintenance in Automotive Manufacturing
India has been a growing hub for automotive manufacturing, and companies are leveraging AI-powered predictive maintenance to enhance their production processes. Mahindra & Mahindra, one of India’s leading automotive manufacturers, has integrated AI and machine learning into its production plants to predict machinery failures and optimize maintenance schedules. This shift from reactive to predictive maintenance has enabled the company to significantly reduce machine downtime and improve overall productivity.
Using sensor-based data and machine learning algorithms, Mahindra can monitor the condition of critical equipment in real-time, ensuring machines are serviced only when necessary rather than following a fixed schedule. This AI-driven approach has allowed the company to extend the life of its machinery, reduce maintenance costs, and ensure that production lines are not interrupted by unexpected breakdowns. As a result, Mahindra has seen improved efficiency and output across its plants, demonstrating the power of AI in driving modern manufacturing.
5. Cloud Manufacturing
What is it?
Cloud manufacturing connects production systems through cloud-based platforms, enabling real-time collaboration and data sharing across global manufacturing facilities.
Impact of Cloud Manufacturing on Modernization
Cloud manufacturing enhances flexibility and scalability by allowing manufacturers to adjust production remotely. It also supports real-time monitoring, making it easier to manage global supply chains, optimize inventory, and quickly respond to changes in demand.
Cloud manufacturing also supports data-driven decision-making, as companies can analyze real-time production data to optimize processes, improve quality control, and minimize downtime. It also makes it easier for manufacturers to scale operations up or down based on demand without significant capital investment in new hardware or facilities.
Strategic Recommendation for Brands
Adopt cloud-based platforms to enhance collaboration and optimize operations across your supply chain. Cloud manufacturing can give your brand the agility to respond quickly to market fluctuations.
6. Digital Twins
What is it?
Digital twins are virtual representations of physical assets, allowing manufacturers to simulate and optimize production processes in a virtual environment before making real-world changes.
Impact of Digital Twins on Modernization
Digital twins cut costs and boost efficiency by enabling manufacturers to test strategies and predict equipment failures virtually, ensuring optimized production with minimal downtime.
Digital twins are also key to predictive maintenance, as they can model wear and tear on machinery, helping manufacturers address issues before they result in equipment breakdowns. This capability significantly improves uptime and reduces operational disruptions. The use of digital twins in manufacturing is a prime example of how data, when paired with simulation technologies, can drive efficiency, innovation, and cost savings.
Strategic Recommendation for Brands
Adopt digital twin technology to simulate and optimize production processes, improving efficiency and minimizing risk. This will help your brand innovate while controlling operational costs.
7. Dark Factories
What are dark factories?
Dark factories are fully automated production facilities that operate 24/7 without human intervention, significantly improving efficiency and lowering labor costs.
Impact on Modernization
Dark factories allow continuous production, reducing time and increasing output. Automation improves precision and minimizes human error, making it ideal for high-tech industries.
Strategic Recommendation for Brands
Consider dark factory automation for highly repetitive or dangerous tasks to boost efficiency, reduce costs, and maintain high precision in your operations.
8. Augmented Reality (AR) and Virtual Reality (VR)
Overview
AR and VR are used in manufacturing for training, maintenance, and product design. AR overlays digital information on physical objects, while VR creates immersive simulations for training and prototyping.
Impact of AR/VR on Modernization
AR and VR technologies improve accuracy and safety by allowing workers to visualize repair instructions and data overlays in real time. VR simulations help manufacturers train workers and test new product designs in a cost-effective, risk-free environment.
AR and VR are also used in product design and prototyping, allowing engineers to experiment with new ideas and test them in virtual environments before moving to physical production. This approach not only reduces costs but also speeds up the innovation process by enabling faster iterations and refinements.
Strategic Recommendation for Brands
Implement AR/VR technologies for maintenance and training to improve precision and reduce downtime. This will help your brand maintain operational efficiency while reducing risk and training costs.
Conclusion
The manufacturing industry stands on the brink of a transformative era, driven by rapid advancements in technology and evolving market demands. The eight trends highlighted—ranging from automation and AI to sustainability and smart factories—are reshaping how manufacturers innovate, produce, and compete on a global scale. Businesses that embrace these trends proactively will be better positioned to enhance efficiency, reduce costs, and meet the needs of an increasingly conscious and connected consumer base.
As the pace of change accelerates, staying ahead will require a commitment to innovation, collaboration, and a willingness to adapt. By leveraging these revolutionary trends, manufacturers can secure a future that is not only resilient but also more efficient, sustainable, and attuned to the needs of the modern world.